انواع کامپوزیت ها و روش های ساخت و تولید آنها عنوان مقاله ای است که به طور کاملا مفصل به کامپوزیت ها و انواع آن و همچنین روش های ساخت و تولید آنها خواهیم پرداخت. كامپوزيتها در ابتدايي ترين شكل خود، سازه هايي هستند كه از به هم پيوستن حداقل دو عنصر تشكيل يافته اند كه خواصي متفاوت از اجزاي تشكيل دهنده خود را دارا مي باشند. در عمل، اكثر سازه ها شامل توده اي از مواد بنام بستر (ماتريس) در كنار نوعي تقويت كننده مي باشند كه بخش تقويت كننده اساسا براي افزايش استحكام و سفتي، به ماتريس اضافه مي شود . تقويت كننده هاي فوق ، معمولا به شكل الياف بكار برده مي شوند(شکل 1). برای اطلاع بیشتر در این مورد مقاله انواع کامپوزیت ها و طبقه بندی آنها را مطالعه کنید.
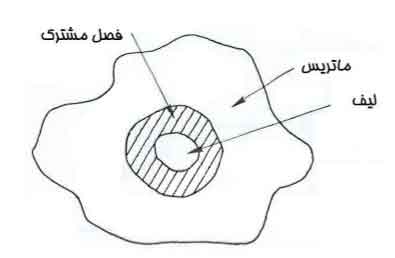
دسته بندی اصلی کامپوزیت ها
- كامپوزيتهای زمینه پلیمری (PMC)
- كامپوزيتهای زمینه فلزی (MMC)
- كامپوزيتهای زمینه سراميكی (CMC)
طبقه بندي كامپوزيت ها
از مواد مختلفي مي توان در ساخت كامپوزيتها استفاده كرد و ظاهراً هم محدوديتي در زمينه انواع تركيبات ممكن وجود ندارد ولي بر اساس شكل مواد داخل كامپوزيت، مي توان آنها را به پنج نوع ذيل تقسيم نمود.
1- كامپوزيتهاي اليافي: كه شامل الياف محاط شده در ماتريس هستند.
2- كامپوزيتهاي لايه اي: كه شامل لايه هايي از موادند كه بر رويهم قرار گرفته اند.
3- كامپوزيتهاي ذره اي: كه شامل ذرات محاط شده در ماتريس هستند.
4- كامپوزيتهاي پولي: ساخته شده از پولك با يا بدون ماتريس.
5- كامپوزيتهاي پر شده: كه از يك ماتريس كه بوسيله ماده ديگري پر شده تشكيل مي شوند. (شکل 2)
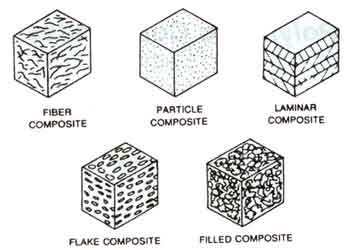
الیاف مورد استفاده در ساخت کامپوزیت ها
اليافي كه در صنعت كامپوزيت استفاده ميشوند به دو دسته تقسيم ميشوند: الف)الياف مصنوعي ب)الياف طبيعي. در کامپوزیتهای چند لایه، میتوان از چند نوع الیاف نیز استفاده کرد که به آنها کامپوزیتهای مخلوط (Hybrid) گویند. (مقاله الیاف هیبریدی و انواع آن ) معمولا سعی میشود از یک نوع زمینه استفاده شود تا چسبندگی خوبی بین لایهها وجود داشته باشد. از الياف متداول در كامپوزيتها ميتوان به شيشه (مقاله الیاف شیشه، انواع آن و نحوه ساخت آنها)، كربن (مقاله الیاف کربن، ساختمان و خواص آن) و آراميد (مقاله الیاف آرامید و خواص آنها) اشاره نمود.
الیاف طبیعی نیز الیافی هستند که از منابع طبیعی مانند معادن، حیوانات و گیاهان بدست می آیند، در گروه الیاف طبیعی قرار می گیرند. الیاف طبیعی را می توان به سه دسته معدنی، حیوانی و گیاهی تقسیم نمود. (مقاله پلیمرها و الیاف طبیعی)
الیاف حجم قابل توجهی از یک کامپوزیت را تشکیل میدهند. وظیفه اصلی آنها تحمل بار اعمال شده به کامپوزیت میباشد. نوع لیف، مقدار آنها و آرایش یافتگی آنها بسیار حائز اهمیتاند و بر خواص زیر تاثیر میگذارند:
- استحکام و مدول کششی، فشاری و خمشی
- استحکام خستگی (Fatigue)
- ضرایب انتقال حرارت و الکتریسیته
- وزن مخصوص کامپوزیت
- قیمت
برای اطلاعات بیشتر در مورد انواع شکل الیاف مورد استفاده مقاله الیاف مورد استفاده در ساخت کامپوزیتها را مطالعه بکنید.
پلیمرهای مورد استفاده در ساخت کامپوزیت ها
در میان پلیمرهای گرماسخت پلی استر غیر اشباع، وینیل استر، فنل فرمآلدهید(فنولیک) اپوکسی و رزینهای پلی ایمید بیشترین کاربرد را دارند. در مورد گرمانرم ها، اگرچه گرمانرمهای متعددی استفاده میشوند، PEEK ، پلی پروپیلن و نایلون بیشترین زمینه و اهمیت را دارا هستند.
همچنین پلیمرهای زیست تخریب پذیر نیز در تولید کامپوزیت ها استفاده می شود که می توانید مقاله پلاستیک ها و کامپوزیت های زیست تخریب پذیر را مطالعه کنید.
روش های ساخت و تولید کامپوزیت ها
همانطوری که در بالا اشاره شد، با يك نگاه كلي به مواد كامپوزيت، متوجه مي شويم مواد اوليه آنها شامل محدوه گسترده اي از انواع رزين ها، الياف و مغزی ها مي باشند كه هر كدام داراي خواص ويژه اي از قبيل استحكام، سفتی، چقرمگي، مقاومت حرارتي، قيمت، سرعت توليد و غيره هستند. با اين وجود، خواص نهايي كه قطعه چند سازه اي توليد شده از اين مواد متنوع، نه تنها تابعي از خواص ويژه مواد اوليه است، بلكه به شيوه طراحي، نحوه بكارگيري، قرار گرفتن در درون سازه و فرآيند توليد نيز وابسته است.
از انواع روش های تولید قطعات کامپوزیتی می توان به روش های زیر اشاره کرد.
- قالبگيری به روش دستی يا لايه گذاري دستی
- قالبگيری با کمک كيسه و خلاء (مكش)
- ساخت قطعات با پیش آغشته ها و اتوکلاو
- پیش آغشته های پخت شونده در دمای پایین
- پخش یا نفوذ ورقه رزین ( RFI )
- قالبگیری با انتقال رزین ( RTM ) (مقاله RTM (آر تی ام)) (مقاله روش های متداول تزریق و انواع جریان در فرایند RTM)
- روش UV-VARTM
- چوب-پلاستیک (مقاله چوب-پلاستیک)
- پالتروژن (مقاله پالتروژن) (مقاله پالتروژن و مشکلات آن) (مقاله تکنولوژی تولید پالتروژن منحنی) (مقاله تجهیزات پالتروژن ترموست)
- وش های تولید قطعات کامپوزیتی از الیاف هیبریدی (مقاله وش های تولید قطعات کامپوزیتی از الیاف هیبریدی)
برای مطالعه بیشتر در مورد معرفی روش، مزایا و معایب هر کدام از روش ها و همچنین کاربرد هر روش برای ساخت خاص خانواده کامپوزیت ها می توانید مقالات زیر را بخوانید.
مقاله روشهای ساخت کامپوزیت ها-بخش اول
مقاله روشهای ساخت کامپوزیت ها-بخش دوم
مقاله روشهای ساخت کامپوزیت ها-بخش سوم
مقاله مقایسه فرایندهای CRTM، VARTM و LRTM
کارایی و خواص کامپوزیت ها
ما باید بدانیم کامپوزیت ماده ای نیست که فقط از اختلاط فیزیکی دو یا چند ماده بوجود آمده باشد بلکه نکته اینست که این ماده جدید، ویژگی های بهتری از هر یک از اجزاء متشکله خود دارد. این شاید مهمترین انگیزه ساخت کامپوزیت ها باشد.
خواصی را که می توان به وسیله بهم آمیختن مواد(کامپوزیت) بهبود بخشید، عبارتند از:
- مقاومت
- سختی
- مقاومت در برابر خوردگی
- جذابیت ظاهری
- وزن
- مقاومت در مقابل خستگی
- انبساط یا انقباض ناشی از تغییرات درجه حرارت
- عایق حرارتی بودن
- عایق صوتی بودن
- قابلیت هدایت حرارتی
- قابلیت هدایت الکتریکی
البته یافتن کامپوزیتی که کلیه خواص فوق را دارا باشد کار دشواری است. معمولا برخی از این خواص در یک کامپوزیت مورد نیاز است.
پارامترهای اصلی موثر در خواص کامپوزیت ها
این پارامترها را می توان به سه دسته زیر طبقه بندی نمود.
۱- موادی که کامپوزیت از آنها تشکیل شده است.
۲- شکل و ترتیب قرار گرفتن این مواد اصلی
۳- اثرات متقابل این مواد بر یکدیگر
برای مطالعه بیشتر در مورد کارایی و خواص کامپوزیت ها، مقاله کارایی و خواص کامپوزیت ها را مطالعه کنید.
مراحل پخت رزین و تشکیل ماتریس در کامپوزیت ها
مراحل مختلف واکنش پلیمریزاسیون در عملیات پخت
بطور کلی، عملیات پخت را که طی آن رزین مایع به جسم کاملا جامد تبدیل می شود را میتوان به سه مرحله مختلف تقسیم بندی نمود. این مراحل عبارتند از ژل شدن(Gelation)، شیشه ای شدن(Vitrification) و پخت کامل(Full cure). حال به توضیح هر کدام از مراحل ذکر شده می پردازیم.
ژل شدن
در اثر واکنش های پلیمریزاسیون، مولکولهای رزین شروع به رشد کرده تا اینکه به نقطه ژل برسد. در این مرحله ویسکوزیته رزین با افزایش وزن مولکولی افزایش می یابد ولی همچنان قابلیت جریانپذیری خود را حفظ می کند. نقطه ژل در واقع نقطه شروع و تشکیل ساختار مولکولی شبکه ای می باشد. وقتی که رزین به این نقطه می رسد ویسکوزیته بشدت افزایش یافته و رزین قابلیت جریانپذیری خود را از دست می دهد.
شیشه ای شدن
با افزایش درصد تبدیل واکنش پس از نقطه ژل، دمای انتقال شیشه ای (Tg) افزایش می یابد تا اینکه درجه حرارت (Tg) رزین بالای درجه حرارت پخت قرار می گیرد. در این حالت رزین به حالت شیشه ای شدن خود می رسد. در این شرایط عملا ماکرومولکولها از حرکت بازایستاده و واکنش پلیمریزاسیون متوقف می گردد. در چنین حالتی رزین به حداکثر درصد پخت خود می رسد. شکل ۱ مراحل مختلف رشد مولکولها از حالت مونومر یا پیش پلیمر تا ساختار کاملا شبکه ای شده را نشان می دهد.
پخت کامل
در فرآیند RTM پس از اینکه قالب توسط رزین پرشد، فاز پخت آغاز می گردد. در این مرحله جریان رزین متوقف شده و رزین از طریق انتقال حرارت هدایتی در مراحل اولیه به درجه حرارت واکنش رسیده و پس از آن واکنش پلیمریزاسیون شروع می گردد. واکنش پلیمریزاسیون با آزاد شدن مقدار قابل توجهی حرارت همراه بوده و باعث پخت نهایی قطعه در داخل قالب می گردد.
برای مطالعه بیشتر در این مورد به مقاله مراحل پخت رزین و تشکیل ماتریس در کامپوزیت ها مراجعه کنید.
برای خواندن همه مقالات مربوط به کامپوزیت ها روی عنوان کامپوزیت در زیر کلیک کنید.
مقاله های تخصصی کامپوزیت
برای دریافت مقالات بعدی سایت ایمیل خود را در فرم زیر وارد کنید.